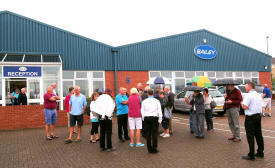 |
The side, roof panel and floor production
line. Showing the construction and materials used. Note the different
GRP used for the shower area. The model being built through out our
visit was the S3 Madrid |
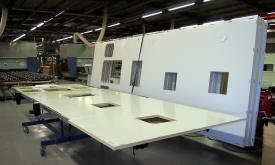 |
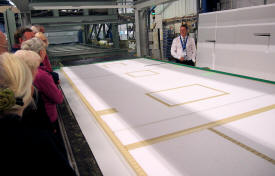 |
|
|
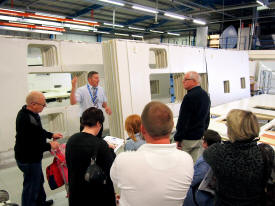 |
|
|
|
|
|
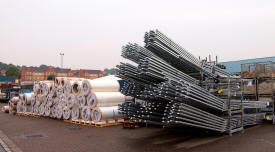 |
|
The Yard with components ready to be used and the stores where we were
demonstrated large item handling. The stores completely changes its
stock every ten days. |
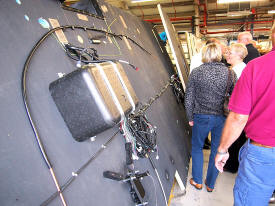 |
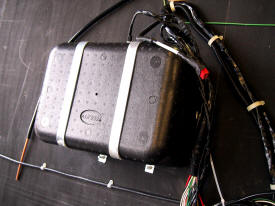 |
The floor unit with the new under slung battery compartment |
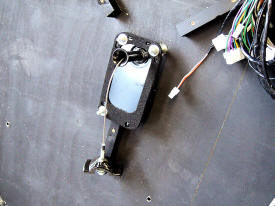 |
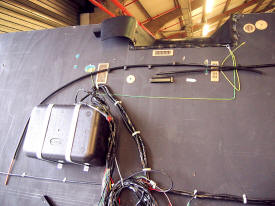 |
the wind down spare wheel system |
|
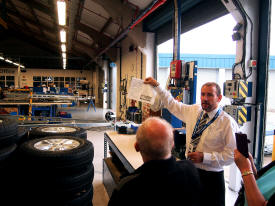 |
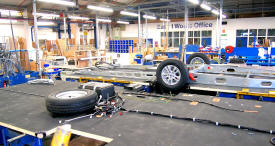 |
Chassis and wheel area. where the chassis is put together and mated with
the floor and wheels |
|
|
|
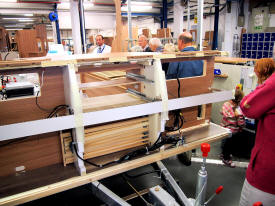 |
|
Starting to add the pre-assembled furniture units |
|
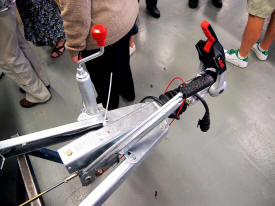 |
|
|
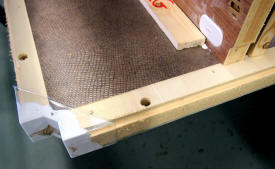 |
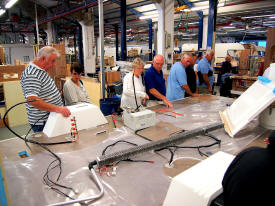 |
Still a wooden floor |
|
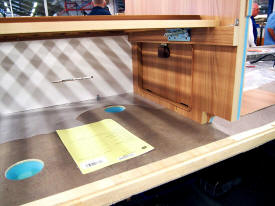 |
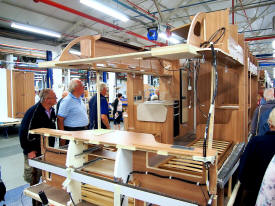 |
The new locker area |
|
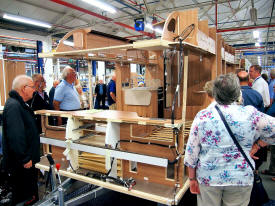 |
|
|
|
|
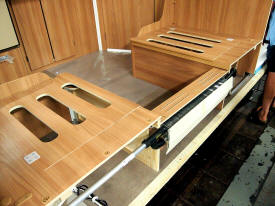 |
New locker area with tray |
|
|
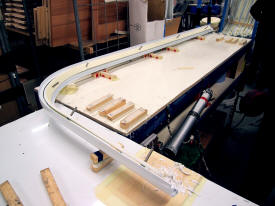 |
Single piece roof and front panel being added and curved |
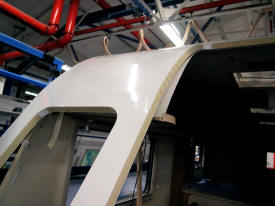 |
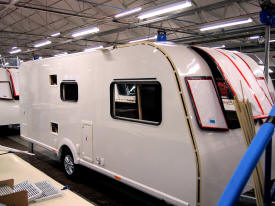 |
|
|
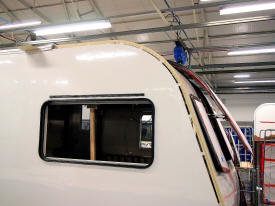 |
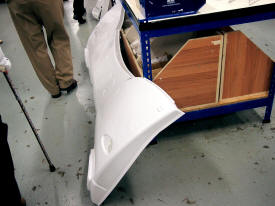 |
|
|
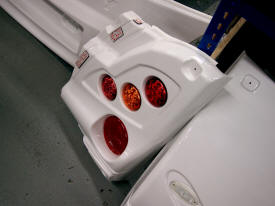 |
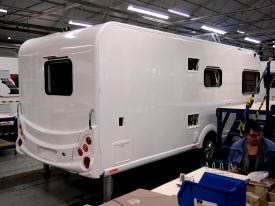 |
The new rear bumper elements |
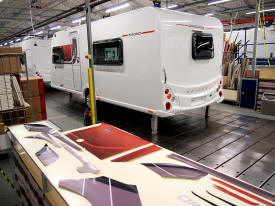 |
|
The finishing line |
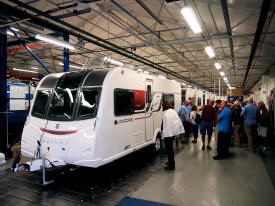 |
|
|
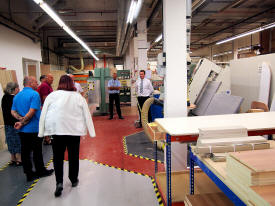 |
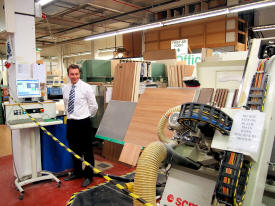 |
furniture machine shop |
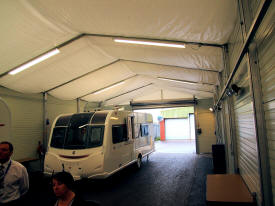 |
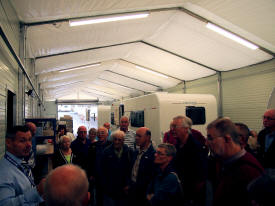 |
The recently added PDI Inspection line. This is new this year and a
great deal of attention is being placed on improving the completed
caravans |
|
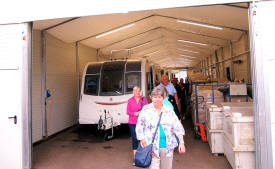 |
One of the check lists used |
|
|
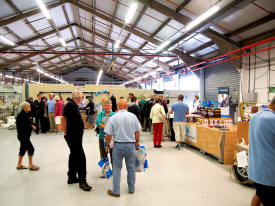 |
We then had a chance to see four of the new Unicorn 3 models and pick up
some bits and pieces. |
|
|
|
I must say that
the Bailey management and staff went out of their way to show us round
and answer questions. They were very honest with us and answered all of
the questions asked. In all there were about 350 visitors and the tours
took most of the day. Thanks' to all of them for this opportunity to see
the new Unicorn S3 being manufactured |