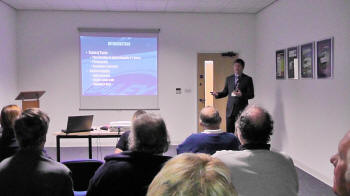 |
Bailey's
Marketing Director, Simon Howard, welcomed us and gave an introduction to
the day and background on Bailey Caravans the company history and
present production. |
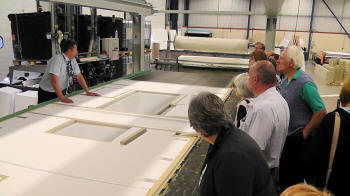 |
 |
The side and roof panel production line.
Showing the construction and materials used. Note the different GRP used
for the shower area. The model being built through out our visit was the
S2 SAVILLE |
 |
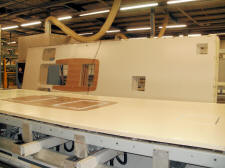 |
|
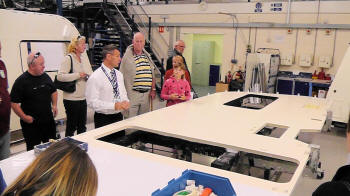 |
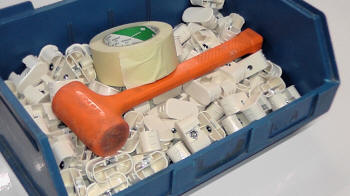 |
The panels after the apertures have been
cut out. The familiar nut retaining components as seen in all Alu-tech
construction. |
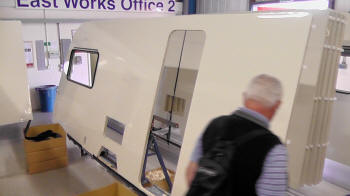 |
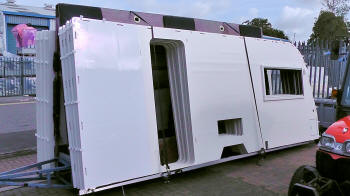 |
The completed side
panels move on to the next stage. |
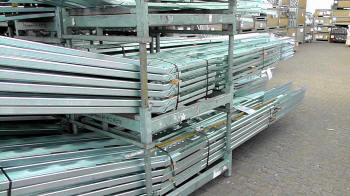 |
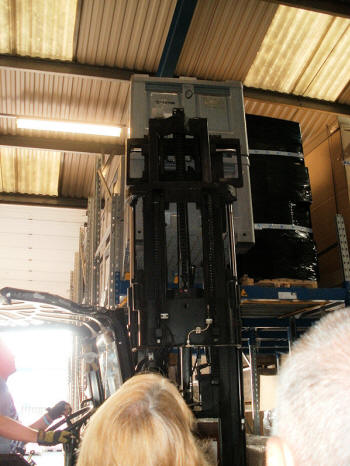 |
The Yard with components ready to be used and the stores where we were
demonstrated large item handling. The stores completely changes its
stock every ten days. |
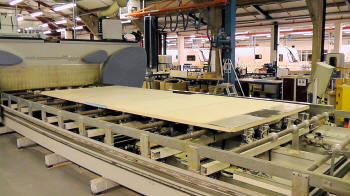 |
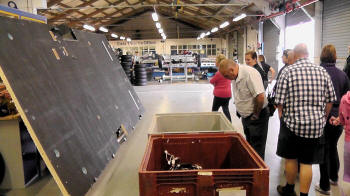 |
The construction of the floor panel |
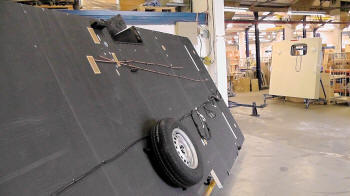 |
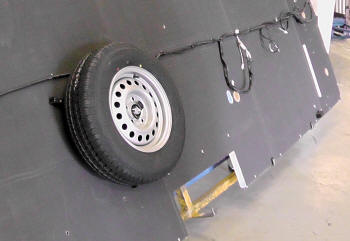 |
and the new wind down spare wheel system |
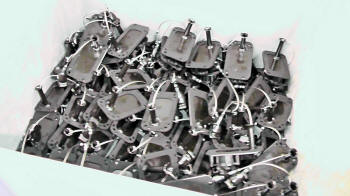 |
Spare wheel mounting modules |
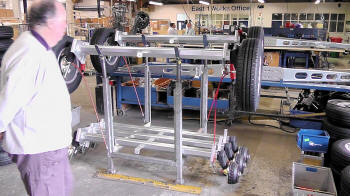 |
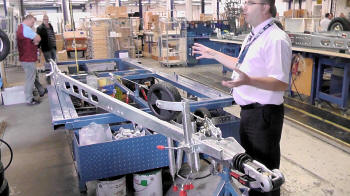 |
The chassis and axle assembly with the
Michelin tyres and balanced wheels. |
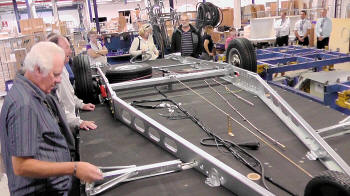 |
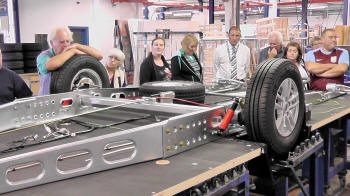 |
The floor is fixed to the chassis |
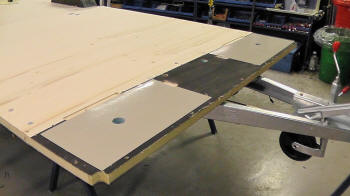 |
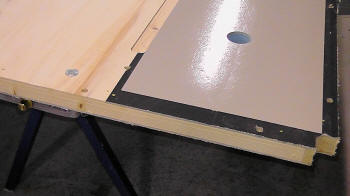 |
The new style construction floor for the
two front lockers |
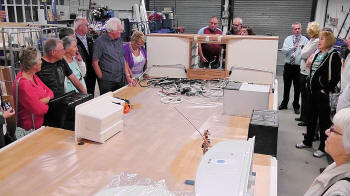 |
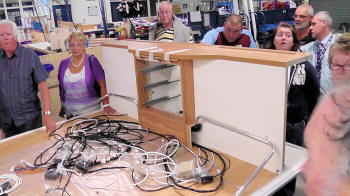 |
The bulkhead is added |
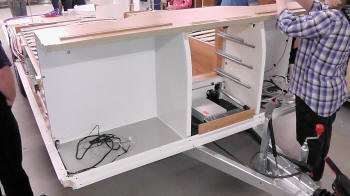 |
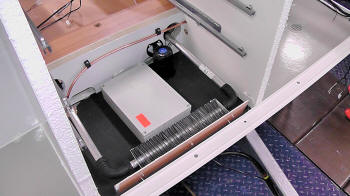 |
Innards of the front lockers and chest
units |
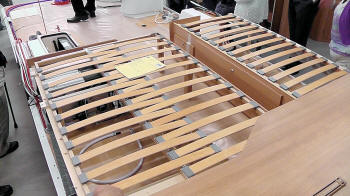 |
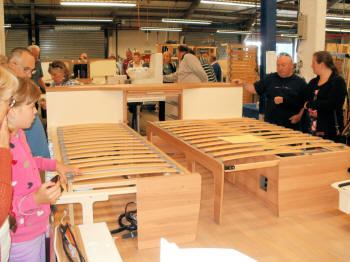 |
The new slatted front seating and bed
bunks pull out assembly is added. |
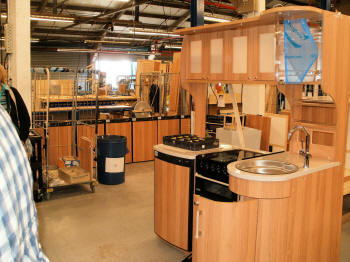 |
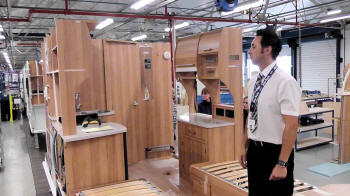 |
and the separately assembled furniture
units placed in position |
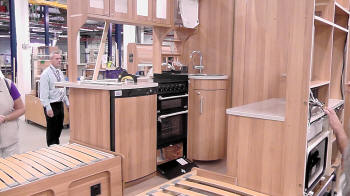 |
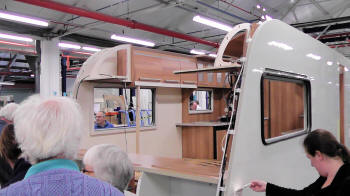 |
and the sides and back panels added. |
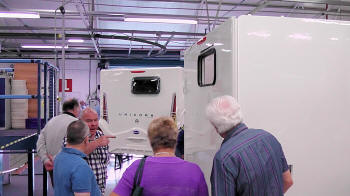 |
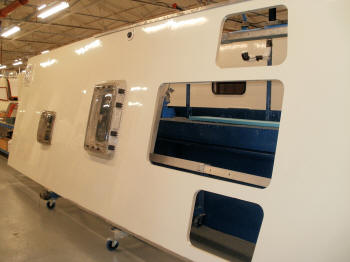 |
The roof and front panel is then positioned and
attached |
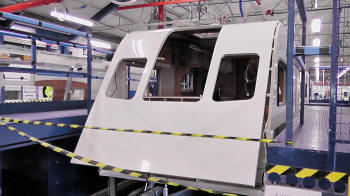 |
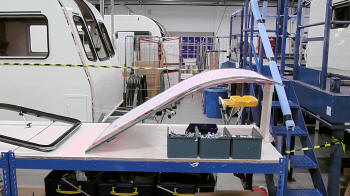 |
with the new front window assembly |
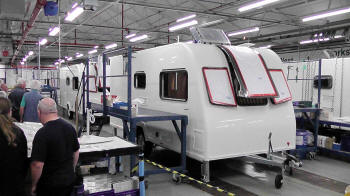 |
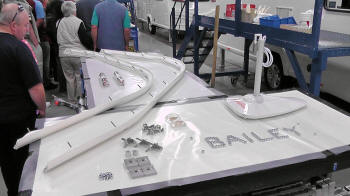 |
all the bits and pieces are then added |
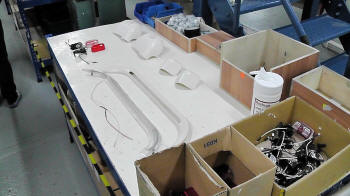 |
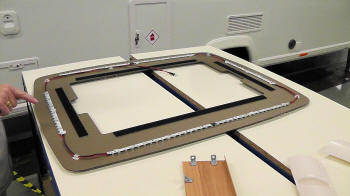 |
including the new LED ceiling assembly |
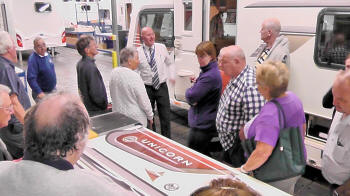 |
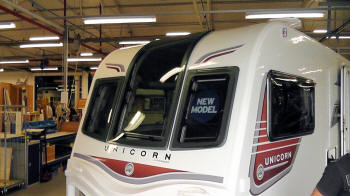 |
and transfers before the new complete
caravan is ready |
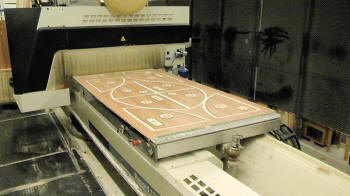 |
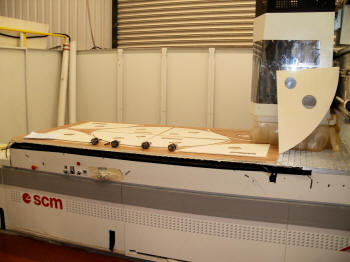 |
The furniture making building with all
the panels being cut out. |
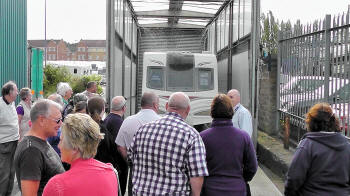 |
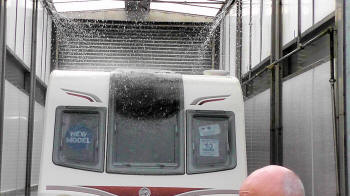 |
The Bailey
factories' unique water testing plant. |
|
|
I must say that
the Bailey management and staff went out of their way to show us round
and answer questions. They were very honest with us and answered all of
the questions asked. In all there were about 350 visitors and the tours
took most of the day. Thanks' to all of them for this opportunity to see
the new Unicorn S2 being manufactured |